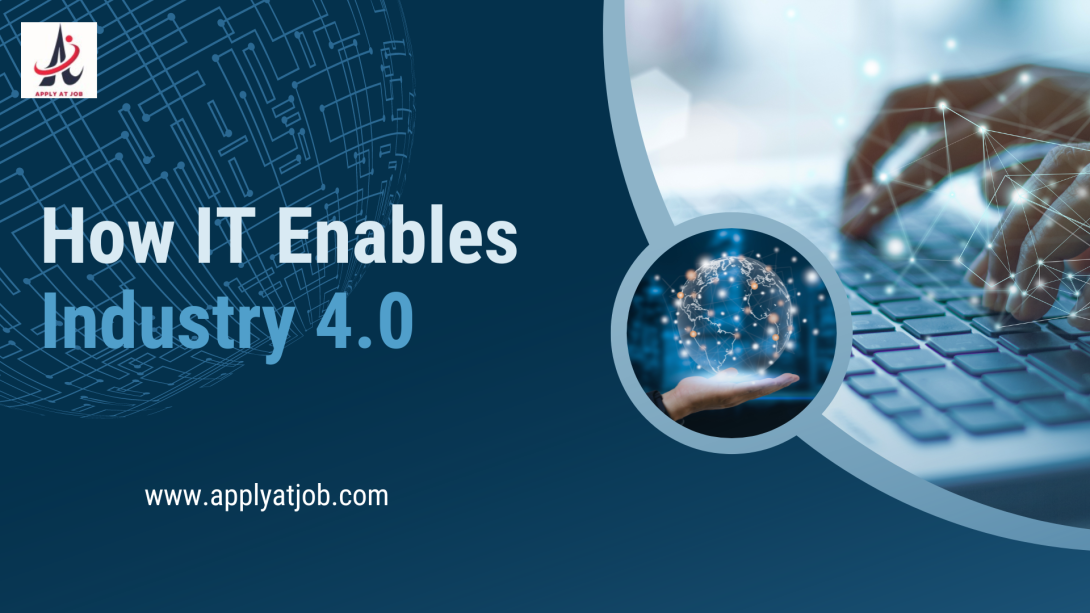
How Technology Facilitates Sector 4.0
Industry 4.0 heralds the advent of a new age in manufacturing and production, driven by the integration of modern technologies like the Internet of Things (IoT), artificial intelligence (AI), big data, and robots. The manufacturing processes, supply networks, and factories are all changing as a result of the fourth industrial revolution, which is creating more intelligent, effective, and flexible production systems. Information Technology (IT) is fundamental to this change. We will examine how IT facilitates Industry 4.0 in this blog by offering the technology, data capabilities, and infrastructure needed to link machines, enhance production workflows, and build more intelligent manufacturing environments.
1. Being aware of Industry 4.0
The Fourth Industrial Revolution, or Industry 4.0, is distinguished by the use of intelligent, self-governing systems that are fueled by data and machine learning. It expands upon the developments of the third industrial revolution, which brought electronics and automation to the production process. But Industry 4.0 goes one step further by facilitating real-time communication between systems, people, and machines, resulting in an automated and completely networked manufacturing environment.
Important aspects of Industry 4.0 include:
. Interconnectivity: Real-time communication between machines, devices, sensors, and people is made possible by the Internet of Things.
. Data-driven: To enhance decision-making and optimize industrial processes, enormous amounts of data are created and evaluated.
. Automation and Robotics: More automation is made possible by cutting-edge robotics and artificial intelligence (AI) technologies, which also lessen the need for manual intervention.
. Smart Factories: Intelligent systems that self-monitor, assess performance, and forecast maintenance requirements are installed in factories.
Industry 4.0 is anchored by IT, which offers the infrastructure and technology required to create smart factories, link devices, and leverage data.
2. How IT Helps to Make Industry 4.0 Possible
IT is essential to realizing Industry 4.0 because it facilitates the incorporation of digital technology into conventional production processes. Here are some of the main domains where Industry 4.0 is made possible by IT:
a)Computing in the Cloud and Edge Computing
Industry 4.0 is supported by cloud computing, which makes it possible to store and handle the massive volumes of data produced by IoT equipment, sensors, and devices. Cloud infrastructure is used by IT departments to control data flow, guarantee system scalability, and offer real-time information access.
Conversely, edge computing moves data processing closer to the manufacturing floor, where it is created. IT departments may guarantee that vital data is handled locally and instantly by utilizing edge computing, which lowers latency and speeds up decision-making in production settings.
How Industry 4.0 is made possible by cloud and edge computing:
. Processing data in real time at the edge for prompt action
. cloud-based, centralized data analysis and storage for long-term insights
. Scalability to manage varying production workloads
b) The IoT, or the Internet of Things
The Internet of Things (IoT) is the backbone of Industry 4.0, establishing a network of interconnected systems that can exchange data and interact by linking machines, devices, and sensors. These IoT systems must be implemented and managed by IT teams in order for them to operate safely and without hiccups. IoT gives firms the ability to follow items as they travel through the supply chain, keep an eye on the condition of their gear, and gather real-time data on their operational performance. Manufacturers may make data-driven decisions that maximize productivity and minimize downtime thanks to this connection.
Utilizing IoT for Industry 4.0:
. Communication between machines to ensure smooth manufacturing
. Monitoring the health and performance of equipment in real time
. using sensor data to inform predictive maintenance to avoid equipment failure
c) Analytics and Big Data
Industry 4.0 relies heavily on big data since smart factories produce enormous volumes of data from a variety of sources, such as IoT devices, machinery, and manufacturing lines. IT is essential to the gathering, storage, and analysis of this data in order to produce insights that may be used to enhance operations. IT teams are able to forecast production results, find patterns, and improve processes with the use of AI algorithms and sophisticated analytics tools. Data analytics, for instance, may be used to estimate demand, cut waste, and enhance industrial quality control.
The importance of big data in Industry 4.0
. Analyzing data in real time to optimize processes
. Demand forecasting and production scheduling using predictive analytics
. Controlling quality with insights derived from data
d) Machine learning (ML) and artificial intelligence (AI)
Industry 4.0 is made possible by AI and ML, which are revolutionary technologies that enable autonomous decision-making, process optimization, and predictive capabilities. AI-powered apps that automate operations, analyze data, and improve production processes without requiring human participation are created by IT departments. Artificial Intelligence is applied in several fields such as robotic automation, machine vision, supply chain optimization, and predictive maintenance. These smart solutions save running costs and improve product quality and manufacturing efficiency.
Industry 4.0 and AI:
. Predictive maintenance to prolong equipment life and minimize downtime
. Autonomous robots that accomplish tasks without human intervention
. AI-powered quality assurance tools that instantly identify flaws
e) Security via cyberspace
Cyberattack risk rises with increased factory and industrial system interconnectivity via IoT and digital technologies. IT teams are essential to the security of Industry 4.0 systems because they put strong cybersecurity safeguards in place to safeguard confidential information, equipment, and intellectual property. IT departments are in charge of enforcing network security, deploying identity management and encryption solutions, and safeguarding Internet of Things devices. The integrity and dependability of Industry 4.0 systems depend on cybersecurity.
Issues with cybersecurity in Industry 4.0:
. Protecting IoT devices from online attacks
. safeguarding private manufacturing information and intellectual property
. putting in place network security procedures to stop illegal access
3. How IT Facilitates the Shift to Intelligent Factories
The "smart factory" is a central idea of Industry 4.0. It is a manufacturing facility that leverages digital technology to automate operations, track performance in real-time, and make data-driven choices. By integrating the required technologies and guaranteeing smooth communication between machines, devices, and systems, IT makes the shift to smart factories possible.
The part IT plays in smart factories
. Data Integration: To make sure that data is available and useable across the production, IT combines many data sources from IoT devices, sensors, and machinery.
. Automation Systems: To enable more efficient production procedures, IT teams create and manage automation systems that operate robots, conveyors, and other equipment.
4. IT's Place in the Industry of Supply Chain Optimization 4.0
applies to supply chains as well as the manufacturing floor. By putting in place technologies that offer end-to-end insight, streamline logistics, and improve communication between suppliers, manufacturers, and distributors, IT makes supply chains more digital.
Important IT contributions to supply chain efficiency include:
. Supply Chain Visibility: IT systems give companies instant access to information about inventory levels, manufacturing schedules, and shipping statuses, enabling them to react swiftly to changes.
. Demand Forecasting using Predictive Analytics: IT departments employ data analytics to predict demand, ensuring that supply chains are adjusted to meet production demands without experiencing either an overstocking or understocking situation.
5. IT's Opportunities and Challenges in Industry 4.0
Although IT makes production digital, it also has difficulties integrating Industry 4.0 technology. Managing the massive volumes of data created, integrating new technologies with existing systems, and maintaining security in increasingly linked settings are some of the major issues.
But there are also advantages to these difficulties. There is an increasing need for IT specialists with knowledge of AI, data analytics, cybersecurity, and cloud computing as more manufacturers implement Industry 4.0. By increasing productivity, cutting expenses, and boosting agility, businesses may obtain a competitive advantage by investing in IT skills:
. Industry 4.0's main IT issues include integrating new technology with existing systems.
. Keeping networked production environments safe from cyberattacks
. handling and evaluating the enormous volumes of data produced by devices and the Internet of Things
Opportunities for IT in Industry 4.0:
. Creating apps for AI and ML to optimize processes
. Using sophisticated analytics to support data-driven decision-making
. assisting in the implementation of smart industrial technology
Conclusion:
Industry 4.0 is propelled by IT, which makes it possible for producers to adopt digital technology and design more intelligent, effective production processes. IT teams are converting conventional manufacturing into networked, automated, and data-driven ecosystems by utilizing cloud computing, IoT, AI, and big data. IT will become more crucial as businesses embrace Industry 4.0 technology in order to guarantee smooth integration, streamline workflows, and protect systems. IT will control production in the future, and companies that make digital transformation investments will drive the next industrial revolution.
You can visit our site: Applyatjob.com
https://applyatjob.com/hiring-employee
https://applyatjob.com/jobs